News & Events
Announcements
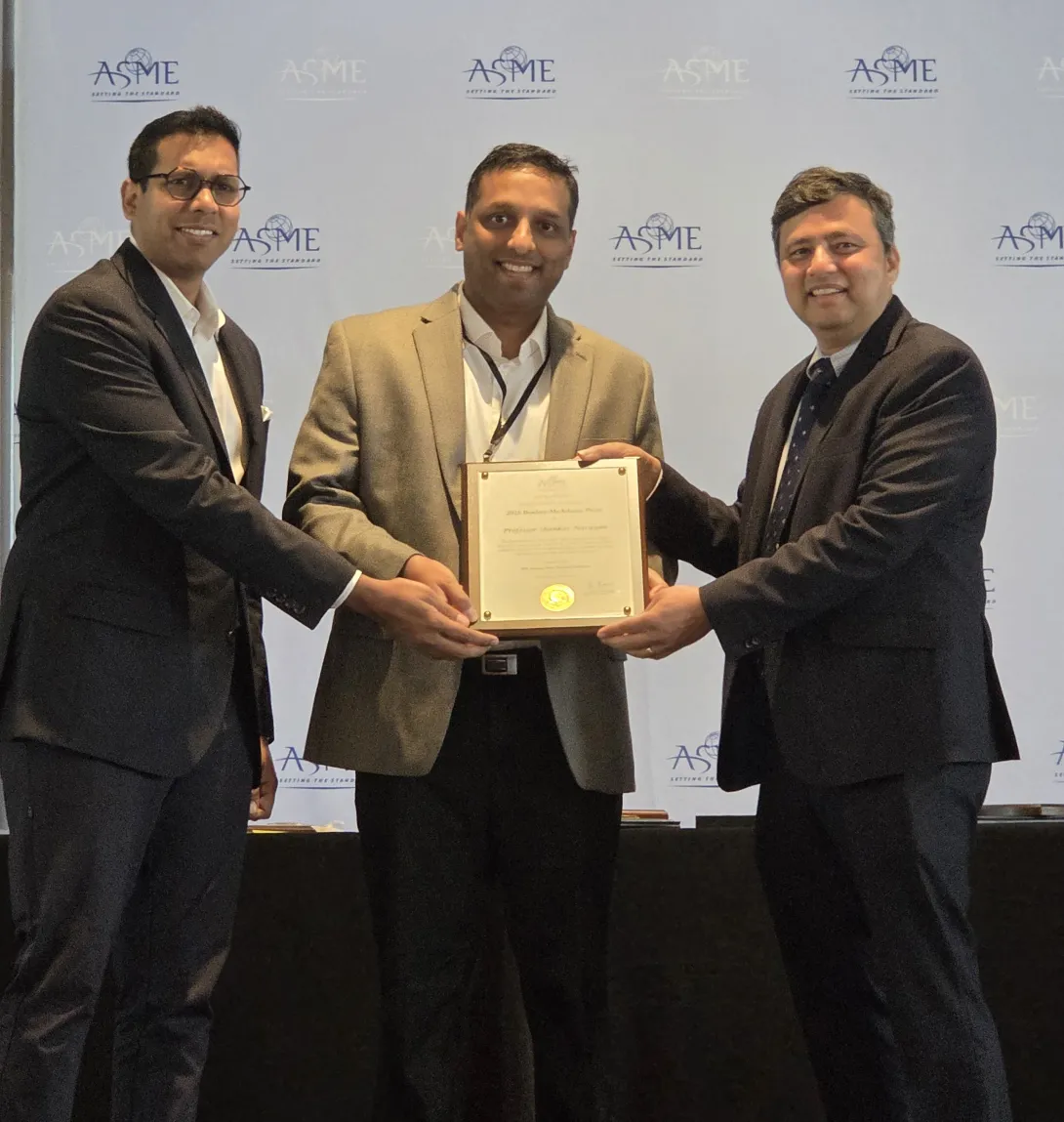
Congratulations to MANE Professor Dr. Shankar Narayan on receiving the HTD Boelter-McAdams Prize at the 2025 ASME Summer Heat Transfer Conference. This award is presented to a member of the Heat Transfer division of ASME that is recognized for their exemplary achievements and contributions to thermal science and engineering.
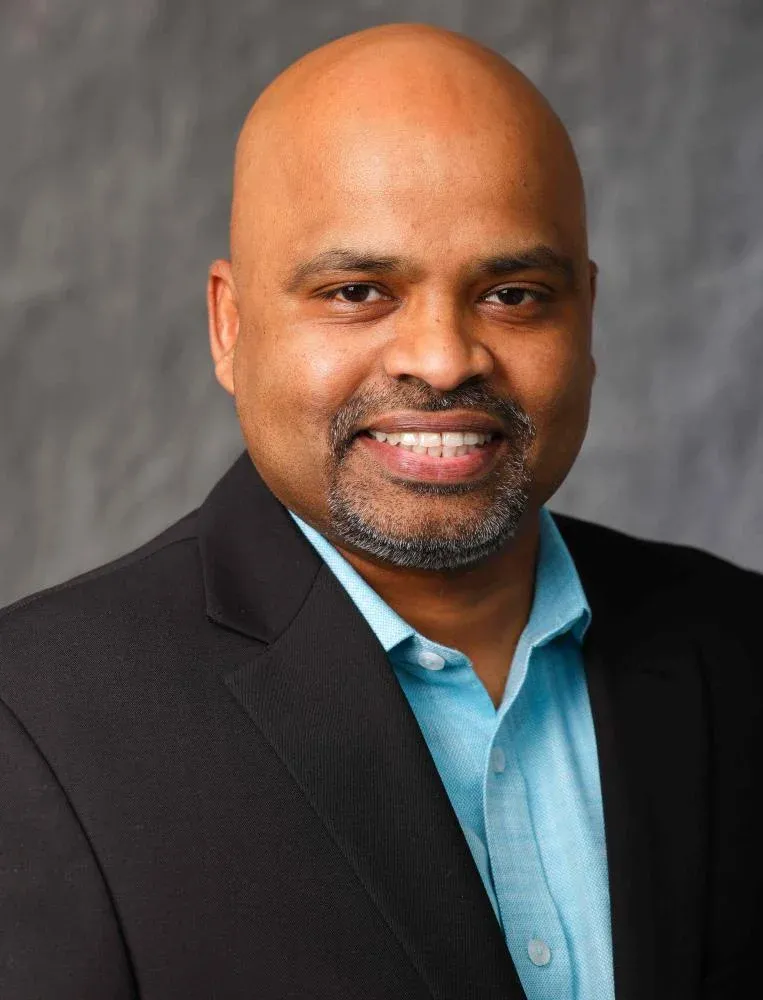
Congratulations to Dr. Johnson Samuel for being awarded the David M. Darrin ’40 Counseling Award for 2025!
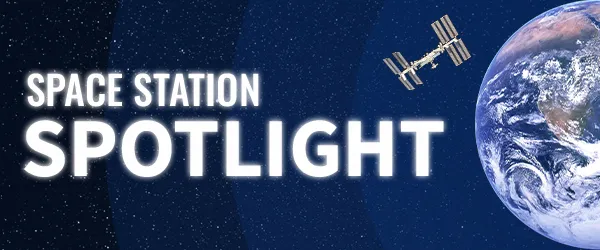
A team of RPI graduates (Joe Adam '17, '18, '21, Tyler Mucci '21, '23, Cesar Gonzalez '20 and Nate Karwic '20) is preparing once again to remotely conduct experiments aboard the International Space Station (ISS). The ring-sheared drop module on the ISS is being utilized to advance our understanding of the flow of complex fluids and develop predictive modeling capabilities.
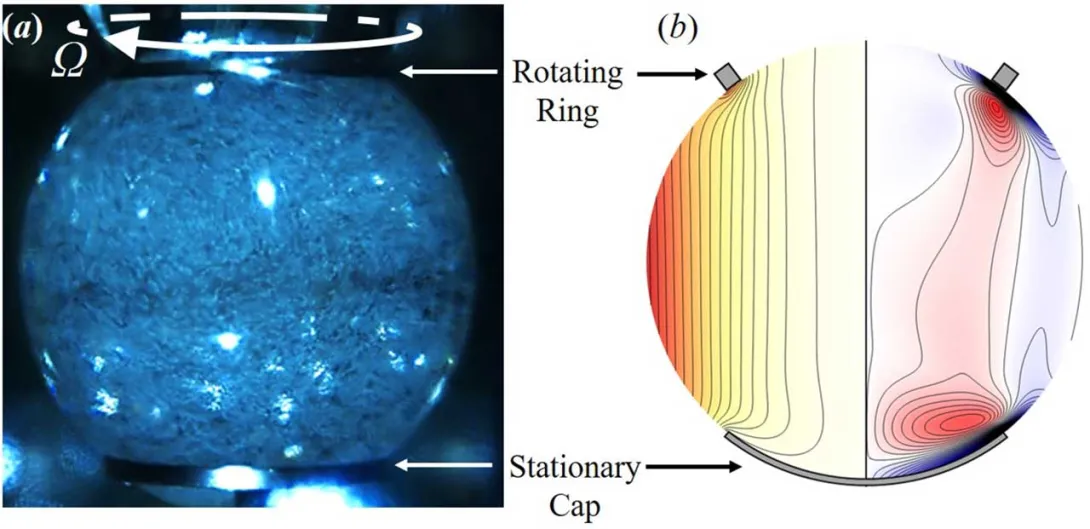
Research on the topic of "Improving Medicine Manufacturing", by MANE Professor Amir Hirsa, and his research lab has been mentioned in an article by ISS National Laboratory titled "NSF-Funded Research Heads to the International Space Station on NASA'S SpaceX CRS 32-Mission". The Rensselaer Polytechnic Institute, with support from Tec-Masters, expanded on prior research to study protein flow and clumping, a key issue affecting the quality of protein-based drugs.
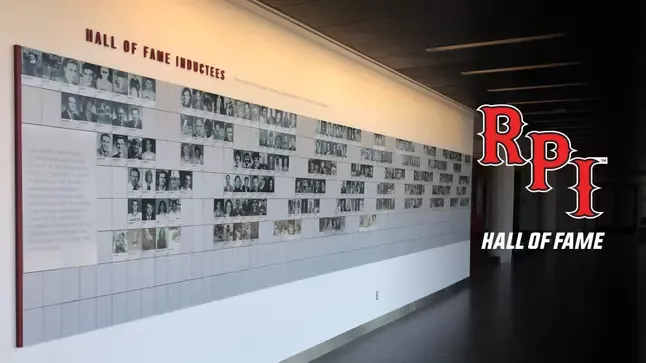
MANE Alumna Jeanne Carboni Debonis '87 is going to be inducted into the RPI Athletics Hall of Fame! Each inductee exemplifies the highest standards of Rensselaer excellence, serving as an inspiration for future generations of student-athletes to pursue greatness—both in their sport and beyond.

Congratulations to Mechanical Engineering senior Shannon Brown who was named the Liberty League Women's Swimmer of the Year! Brown claimed victory in two individual events and anchored two winning relays at the 2025 Liberty League Championship, earning Swimmer of the Meet honors for the second consecutive year.
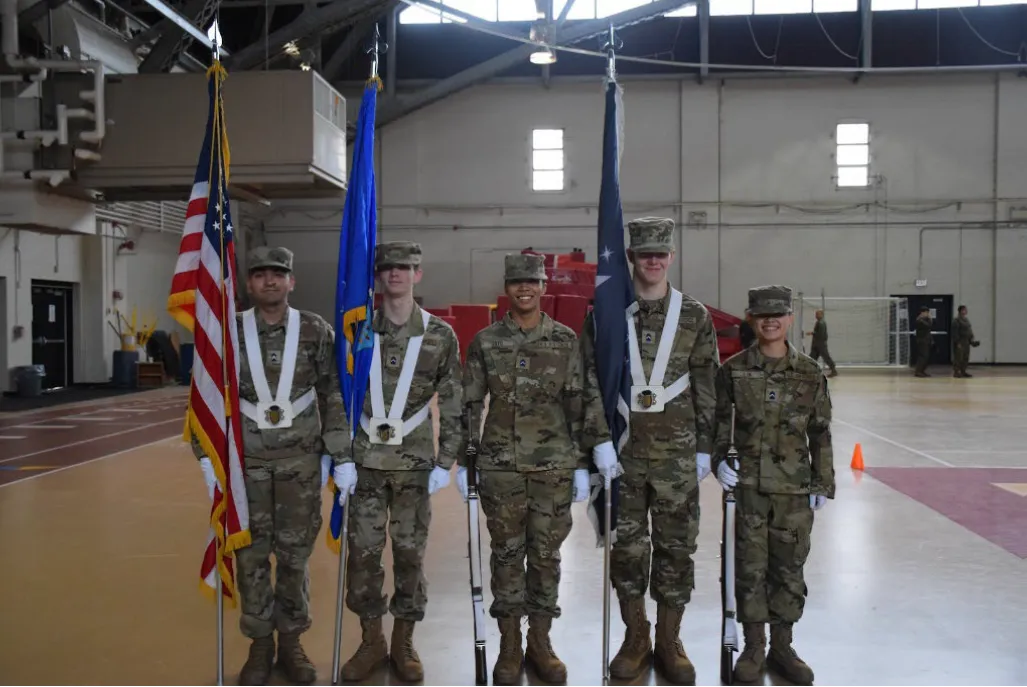
Congratulations to MANE students Christian Blanco, Andrew Hanson, and Jada Lin, members of The Silver Falcons Honor Guard representing Air Force ROTC Detachment 550 at RPI who took top honors at the annual Rensselaer Rumble Military Excellence Competition on February 1, 2025.
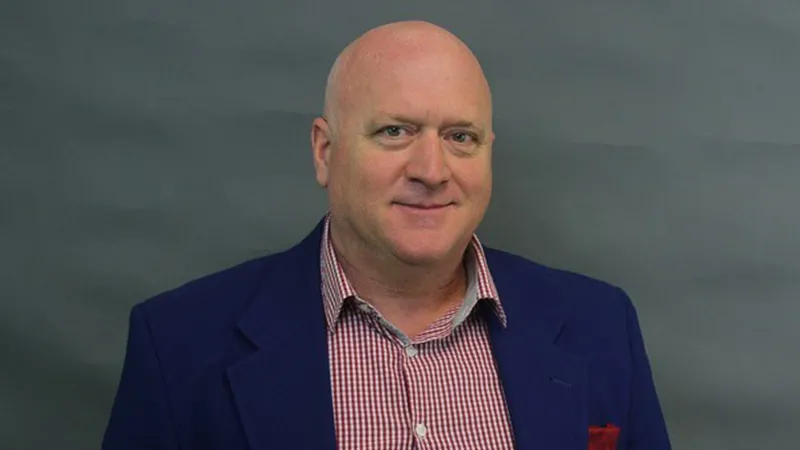
Clint Ballinger, Ph.D., professor of practice in the Department of Mechanical, Aerospace, and Nuclear Engineering (MANE) at Rensselaer Polytechnic Institute, is among 170 inventors elected by the National Academy of Inventors (NAI) to its 2024 Class of Fellows. Read the entire article here
Attend an information session to learn about exciting research opportunities, program requirements, funding options & application processes to MANE's Co-terminal, traditional and part-time Master's programs, and the Accelerated BS-PhD program.
Thursday, February 6th
Noon – 1:00 p.m.
JEC-3117
Tuesday, February 11th
4:00-5:00 p.m.
JEC-3117
Wednesday, February 26th
3:00 – 4:00 p.m.
JEC-3117
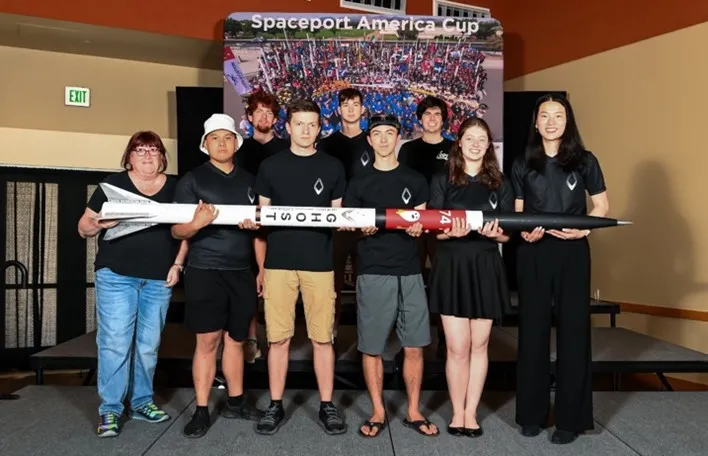
Congratulations to the Rensselaer Rocket Society Ascendants who took 2nd place at the 2024 Spaceport America Cup in the 30k SRAD Solid Motor category. Their rocket reached Mach 1.8 and 30,569 ft with a 30,000 altitude goal, closest to the target altitude in completion.
News
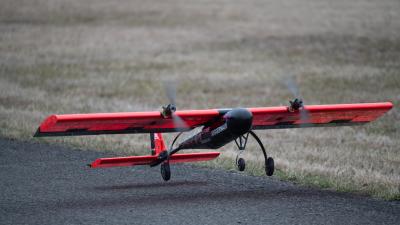
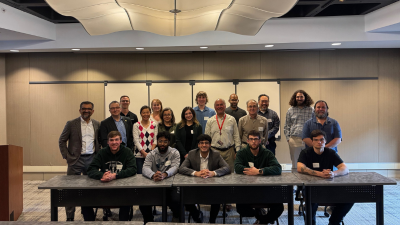
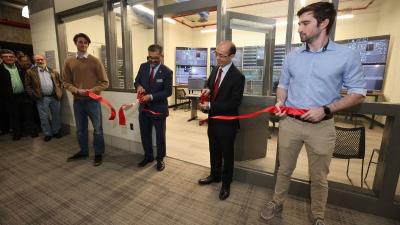
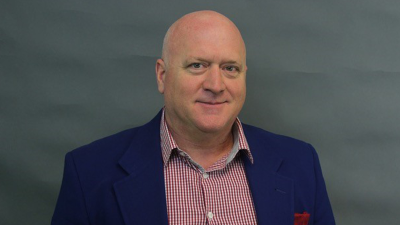
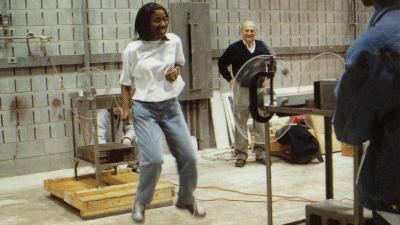
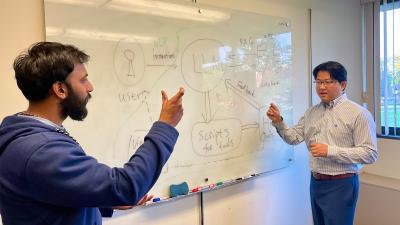
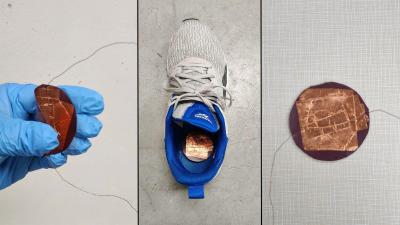
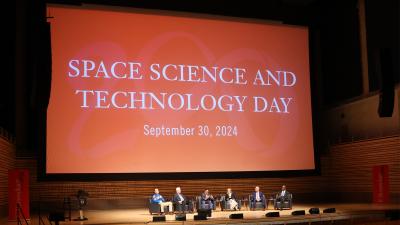
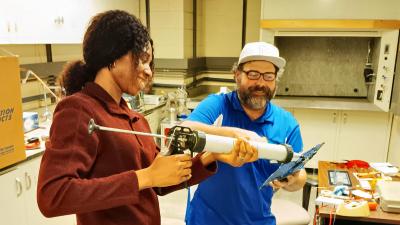
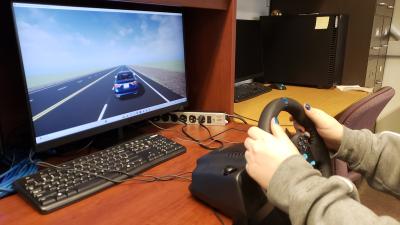